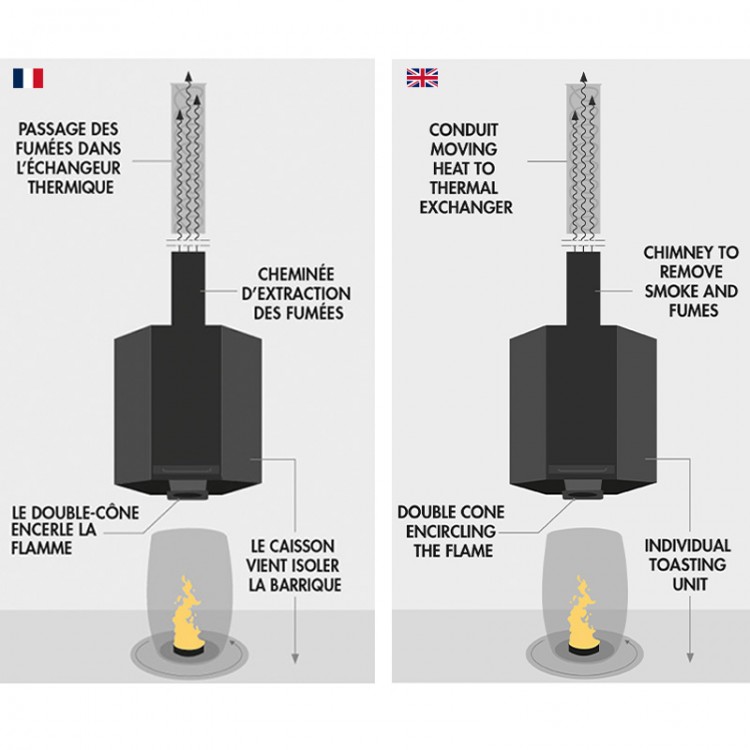
A pioneer of innovation, Vicard Cooperage continues to revolutionize the cooperage world with ongoing improvement of its manufacturing processes. The latest improvement is the installation of a thermal waste recovery technology. As part of its Corporate Social Responsibility policy, Vicard Cooperage is focused on combining performance and innovation with a positive impact on society. Reducing its energy footprint and controlling the use of resources is one of its highest priorities. The first element of response: the recovery of wasted thermal heat from the coopering process.
WASTED HEAT ENERGY, WHAT EXACTLY IS IT?
The wasted heat energy, indirectly produced by a production site, is not initially intended to be recovered or upgraded. However, for a company like Vicard cooperage, setting up such an installation on its site allows it to benefit from a thermal resource already available, thus offering the possibility of improving its energy efficiency and reducing its carbon footprint.
RECOVERY OF HEAT WASTE
All this is possible thanks to our automated toasting by radiant heat. Unique in the industry, the cooperage employs 60 individual units to toast barrels. Each unit channels heat upward into a smokestack which was previously vented to the outside. With the new system, the waste heat is recovered and recycled. “The heat generated represented a large calorific potential, so we were committed to finding a way to utilize it. Not only in view of current environmental issues, but also to reduce our carbon footprint” explained Jean-Charles VICARD.
The cooperage carried out a feasibility study beforehand with ADEME (1). These discussions have resulted in this important project, both for the environment and for the company. Heat exchangers with a power of 500Kw were installed in the boiler room of the cooperage, to recover the calories contained in the heat of its chimneys. The heat present in these conduits (130°C on average) is reused to preheat a water network covering all the needs of the cooperage (hot water, steam, heating...).
OPTIMISATION OF MANUFACTURING PROCESSES
With this system, we estimate that we can reduce our main boiler consumption by 20%. We’re already seeing a positive impact on our steam production rate. We can also further optimize our production process for barrels and large containers (bending, leak checking). The development of this energy also opens new possibilities for the use of steam. An electricity-generating turbine will soon be installed at their production site in Cognac.
(1) ADEME : French Environment and Energy Management Agency